Join Our Groups
TOPIC 8: EXTRACTIONS OF METALS
Occurrence and Location of Metals in Tanzania
Locations of Important Metal Ores in Tanzania
Identify locations of important metal ores in Tanzania
Most metals are found naturally as compounds called minerals. Rocks are made up of crystals of metals. An ore is a rock that contains enough of a metal compounds for it to be worth extracting the metal. The most common ores contain oxides. An example is the ore haematite, which contains iron (III) oxide. Some contain other metal compounds. Malachite contains copper (II) carbonate.
Tanzania is blessed with an assortment of minerals. The mineral found in Tanzania include gold, which is found in Geita (Mwanza), Kahama (Shinyanga), Nyamongo, Buhemba and Majimoto (Mara), and Nzega (Tabora). Large deposits of iron occur at Liganga in Ludewa (Iringa). Copper is found in Mpanda (Rukwa). We also have sodium which occurs in the form of sodium chloride, at Uvinza (Kigoma), in the form of soda ash (Na2CO3) in lake Natron, as a rock salt in Kilwa and as a dissolved salt (NaCl) in sea water.
The Abundances of Metals in the Earth’s Crust
Compare the abundances of metals in the earth’s crust
Metals occur in the sea and in the earth. The form in which they occur depends on their reactivity. The most reactive metals are extracted from the sea. Calcium is extracted from limestone, chalk and marble in the sea. Metals of medium reactivity are found in the earth in form of oxides and sulphides. Examples of these metals include aluminium, zinc, iron and tin. Least reactive metals such as silver and gold occur as free uncombined elements.
We obtain most of the metals we use from the earth’s crust. The majority of metals are too reactive to exist as natural elements. They are found as compounds in ores. The chief ores in order of their economic importance are oxides, sulphides, chlorides and carbonates.
The most common metal is aluminium, which makes about 7.8% of the earth’s crust, followed by iron, which accounts to approximately 4.5%. Others include calcium (3.5%), sodium (2.5%), potassium (2.5%) and magnesium (2.8%). The remaining metals make about 3% of the earth’s crust.
Chemical Properties of Metals
The Difference between Physical and Chemical Strengths of Metals
Differentiate the physical and chemical strengths of metals
Metals are known to have a greater tendency to lose electrons in the course of which they go into solution as ions. A metal, therefore, may be defined as an element which can ionize by electron loss. The number of electrons lost per atom is the valency of the metal and the ion carries an equal number of positive charges, as:
- Na →Na+ + e- (univalent)
- Mg →Mg2+ + 2e- (divalent)
- Al →Al3+ + 3e- (trivalent)
The following are important chemical properties of metals:
- They react with oxygen to form oxides. For example, magnesium burns in air to form magnesium oxide. Metal oxides are bases, which mean they react with water to form an alkaline solution and with acids to form salts.
- Metals form positive ions when they ionize. Consider the ionization of sodium, magnesium and aluminium in the above equations in which case ionization resulted into Na+, Mg2+ , and Al3+ ions respectively. However, there are some exceptions. For example, hydrogen is a non-metal which forms positive ions in solution, H+. This is the only exception in this case.
Physical strength is different from chemical strength. Physical strength is tensile strength of the metal. There are metals with high tensile strengths like iron, copper and aluminium. Other metals like sodium and potassium have low tensile strengths..Chemical strength is the reactivity of the metal. Sodium and potassium have very low tensile strengths but they are the strongest metals chemically.
Sodium and potassium are very weak physically. Sodium is very soft metal and can be cut easily with a knife. It melts at 98oC. It is so light that if floats on water, but it reacts immediately with the water forming an alkaline solution. When freshly cut, it has a silvery lustre but rapidly furnishes due to its reaction with atmospheric carbon dioxide and moisture.
Potassium is a white metal with lustre. It melts at 63oC. Like sodium, potassium is a very light metal and it can also float on water, with which it reacts to form an alkaline solution.
However, sodium and potassium are among the strongest metals chemically. These metals are very reactive and they are always found combined with other elements. The metals are so reactive that they will combine with any non-metal nearby. They never occur free in nature. Both sodium and potassium are so reactive that they have to be stored under oil to prevent them coming into contact with water or air.The compounds of sodium and potassium are quite abundant in nature.
The reactivity and tensile strengths of some metals
- Calcium:Calcium is amongst a group of metals that are too reactive to occur in the free state. It occurs mainly as carbonate, sulphate, fluoride and silicate. It is a soft, greyish metal. In comparison with potassium and sodium, it has a lower tensile strength and high density.
- Iron:Iron is a typical metal. Its density is 7.87. It melts at 1530oC. Iron is a moderately reactive metal. The metal reacts with excess steam at red heat to produce triiron tetraoxide.
- Copper Copper is a less reactive metal. It is a red-brown metal with a lustre. It can be polished. Its tensile strength is fairly high. When heated in air, copper forms a layer of black copper (II) oxide on the surface: 2Cu(s) + O2(g)→2CuO(s)It reacts with hot concentrated sulphuric acid to form copper (II) sulphate and liberate sulphur dioxide. Cu(s) + 2H2SO4(aq)→CuSO4(aq) + 2H2O(l) + SO2(g)
The table below compares the tensile strengths of calcium, iron and copper metals.
Tensile strengths, densities and melting points of calcium, iron and copper
Calcium | Copper | Iron | |
Tensile strength | Low | Fairly high | High |
Melting point (oC) | 850 | 1080 | 1535 |
Density (g cm-3) | 1.55 | 8.95 | 7.9 |
The Reducing Power of Different Metals
Compare the reducing Power of different metals
As we learned early, metals tend to lose electrons during chemical reactions. This process of losing electrons is called oxidation. Metals normally lose electrons to non-metals, which accept those electrons. Therefore, metals are said to be electron donors while non-metals are electron acceptors. In this case, metals can be termed as reducing agents, because they donate electrons which, when accepted by non-metals, tend to lower their oxidation numbers. Non-metals are called oxidizing agents, because they oxidize or increase the oxidation number of metallic atoms through accepting the electrons donated by metals.
Metals differ in the ease of losing the electrons, depending on their electronic configurations. This is because; it is only the outer electron(s), which take part in a chemical reaction. The nucleus of an atom, being positively charged, normally attracts the electrons towards itself, hence making the electrons difficult to remove from their shells. The further the electrons are from the central nucleus, the easier it is removing them from their shells and vice versa. Therefore, atoms with larger atomic radii donate their electrons more easily than those with small atomic radii.
For example, compare the electronic configuration of sodium (2:8:1) with that of potassium (2:8:8:1). Sodium ionizes by losing one electron from its outer shell to attain the structure of the nearest noble gas (2:8). Likewise, potassium ionizes by losing one electron from its outer shell to attain the noble gas structure, 2:8:8. But, in which of the two cases is it easy to remove electron and why? It is easy to remove the electron from the outer shell of potassium than sodium because the atomic radius of calcium is too large as compared to that of sodium. This is because in calcium the outer electron is more loosely held by the central nucleus and hence easy to remove from its shell. This is true because the ability of the nucleus to hold the electrons firmly depends on the distance of the electrons from the nucleus.
Metals that release the electrons more readily are said to be strong reducing agents compared to those that release their electrons least readily. For example, potassium with an electronic configuration of 2:8:8:1 is a stronger reducing agent than sodium, which has an electronic configuration of 2:8:1.
Therefore, it is clear that when atoms of elements lose electrons from their outermost shells, they obtain octet or doublet structures and hence become chemically stable. It is not easy to remove electron(s), by ordinary chemical means from such stable noble gas structures.
From the context of the above explanations, the reducing power of a metal can be defined as its readiness to release electrons from its outer shell. Metals whose atoms release electrons more readily have high reducing powers than those metals whose atoms do not readily release their electrons.
Reactivity series of metals
Reactivity series refers to arranging or listing the metals in order of reactivity. The reactivity series are obtained by consideration of the action of air, water and acids on the metals, and how easily the oxides of these metals can be reduced. Consider the table of reactivity series below (Table 8.2). Oxides of the first group of five metals cannot be reduced by carbon. Those of the second group of three metals can react with acids, displacing hydrogen. The third and last group comprises of least reactive metals. In table 8.2, the metals are arranged in order of reactivity series. It indicates the inverse order in which the elements were isolated. Thus, metals low in the series such as gold, silver and lead have been known since early times. Metals high in the series proved very difficult to isolate. It was Davy’s work on electrolysis that led to isolation of potassium, sodium, calcium, magnesium and aluminium over a period of years from 1807, when Davy isolated potassium and sodium, to about 1850, when aluminium was isolated.
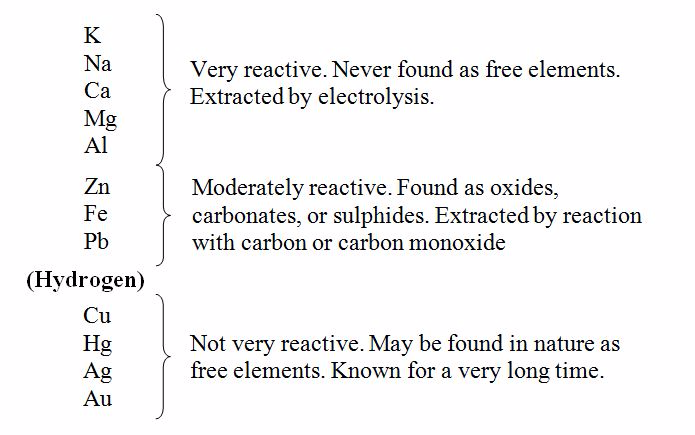
The reactivity series of metals
Metals low down in the series are frequently found as the free elements, although they may also be obtained from ores because the amounts found as the free metal are not sufficient for industrial purposes. Gold, however, the last element of the series is found and mined almost entirely as the free element.
Generally, it is these relatively uncreative metals that we find the most uses for. Iron and copper, for example, can be found in many household and everyday objects.Metals higher up in the series are more reactive than those lower down. A metal higher up in the series will displace a metal lower down from a solution of one of its salts. For example, iron will displace copper from its salt.
Fe(s) + CuSO4(aq)→ Cu(s) + Fe SO4(aq)
Zinc and iron will displace hydrogen from dilute acids such as dilute hydrochloric acid or dilute sulphuric acid.
Zn(s) + 2HCl(aq) →ZnCl2(aq) + H2(g)
Fe(s) + H2SO4(aq) →FeSO4(aq) + H2(g)
Copper has no reaction on either dilute sulphuric acid or dilute hydrochloric acid. With hot concentrated sulphuric acid, sulphur dioxide is liberated and copper (II) sulphate is formed.
Cu(s) + 2H2SO4(l) →CuSO4(aq) + 2H2O(l) + SO2(g)
Useful things to remember about the reactivity series
- The more reactive the metal, the more compounds it forms. So only copper, silver and gold are ever found as free elements in the earth’s crust. The other metals are always found as compounds.
- When a metal reacts, it gives up electrons to form ions. The more reactive the metal, the more easily it gives up electrons.
- The more reactive the metal, the more stable its compounds are. Stable means difficult to breakdown. For example, when you heat sodium nitrate you get sodium nitrite:2NaNO3(s)→ 2NaNO2(s) + O2(g)But copper (II) nitrate breaks down further, to oxide, giving off nitrogen dioxide:2Cu(NO3)2(s)→ 2CuO(s) + 4NO2(g) + O2(g)
- The more reactive the metal, the more difficult it is to extract from its compounds (since the compounds are stable). For the most reactive metals, you will need the toughest method of extraction: electrolysis.
- The less reactive metals have been known and used since ancient times, because they are easiest to extract.6. If you stand two metals in an electrolyte and join them up with a copper wire, electrons will flow from the more reactive metal to the less reactive one.
Extraction of Metals by Electrolytic Reduction
The Criteria for the Choice of the Best Methods of Extracting a Metal from its Ore
Outline the criteria for the choice of the best methods of extracting a metal from its ore
Most metals are naturally found in compounds called ores. The metals are obtained from the ores by a process called extraction.The extraction consists of separating the metal from minerals in the ore
A few metals are found “native”. This means that they are uncombined with other elements, for example, silver and gold.To extract ores containing minerals, a chemical reaction must be used to separate the metal from other elements. The choice of the best method for extraction of a metal from its ore depends on the chemical reactivity of the metal to be extracted. Most ores contain metal oxides. To extract the metal, oxygen must be removed from it. This reaction if called reduction.
Because the metal is always the most electropositive part of an ore, and so has a positive oxidation state, the formation of the free metal from its ore is always a reduction.
Mn+ + ne- →Mo
Very reactive metals like sodium and potassium are strongly bonded in their ores. The more reactive the metal is the more stable its compounds are, and the more energy is needed to break down the bond between the metal and oxygen. Therefore, the extraction of these metals requires a strong method of reduction: electrolysis (or electrolytic reduction).
Hence, metals at the top of the reactivity series are obtained from their ores by electrolysis (electrolytic reduction). Electrolysis is a more expensive process than reduction with carbon or carbon monoxide. However, it is the only economic way to obtain metals such as aluminium. For less reactive metals at the middle of the reactivity series, the oxygen can be removed by chemical reduction with carbon or carbon monoxide. This method is used for extraction of metals such as zinc, iron and copper as shown and discussed in table 8.3. Least reactive metals such as copper, silver and gold may be found in uncombined state.
Methods of extraction of different metals from their ores
Metal | Method of extraction from ore |
Potassium | Electrolysis |
Sodium | |
Calcium | |
Magnesium | |
Aluminium | |
Zinc | Chemical reduction with carbon or carbon monoxide |
Iron | |
Lead | |
Copper | Roasting in air |
Silver | Occur naturally as elements |
Gold |
Stages of the extraction of moderately reactive metals
There are four main stages for the extraction of moderately reactive metals:
- Mining and concentration of the ore
- Roasting in air
- Reduction of oxides to metals
- Purifying the metal
Mining and concentration of the ore
Mining is just the first step. The ore must then be decomposed to give the metal. This is called extraction.The unwanted rock material in the ore is called gangue. The ore is treated to remove as much gangue as possible. For example:
- It is crushed and washed. In this case, the ore is broken down into small pieces, which are then grinded down to fine powder. Then it is either dropped into water, where the fragments containing the metal sink faster or jets of air are blown at it, where the lighter waste material is carried to one side.
- A method called froth flotation is used with sulphide ores (e.g. CuS or ZnS). The ore is powdered, fed into water tanks and made into slurry with water. Then “frothing” chemicals (a suitable oil) are added. Sulphides are attracted to these chemicals. When air is blown through the slurry, froth rises to the top of the tank carrying the metal sulphides with it. They are skimmed off and dried. The gangue sinks.
- Magnetic separation can be used. The iron ore can be separated from other material in the crushed ore by using electromagnet.
Roasting in air
For the ores that occur as sulphides or carbonates of the metal, the concentrated ore is heated (roasted) in air to convert the ore into an oxide, for example:
- 2PbS(s) + 3O2(g)→ 2PbO(s) + 2SO2(g)
- 2ZnS(s) + 3O2(g)→ 2ZnO(s) + 2SO2(g)
- ZnCO3(s)→ ZnO(s) + CO2(g)
It is usual to convert sulphides and carbonates into oxides before reduction because oxides are more easily and efficiently reduced than sulphides. The oxides resulting from roasting (heating) the sulphides or carbonates in air are then reduced chemically with carbon or carbon monoxide.
Most copper is extracted from copper pyrites, CuFeS2. The ore is roasted in a limited supply of air to produce to produce copper (I) sulphide:
2CuFeS2(s) + 4O2(g) → Cu2S(s) + 3SO2(g) + 2FeO(s)
The copper (I) sulphide is then reduced to copper by heating in air: Cu2S(s) + O2(g) → 2Cu(s) + SO2(g)
The copper produced by this method is never pure. It must be refined (purified) by electrolysis if it has to be used for electrical wiring.
Reduction of oxides to metals
This is another important stage in the extraction of metal. Here, the roasted ore must now be reduced to respective metals. Reduction occurs at a very high temperature. The materials employed for reduction are mainly carbon or carbon monoxide. Thus;
Fe2O3(s) + 3CO (g) →2Fe (l) + 3CO2(g)
ZnO(s) + C(s) →Zn(s) + CO(g)
Purification (Refining)
Very often, the product of the reduction process is never pure. The product has to be purified first before being put into use. Purification is normally done through a number of ways, which include:
- Electrolysis: Electrolysis is used to produce a pure metal directly from its molten compounds. Examples of metals which are purified by electrolysis are copper and zinc. Copper produced in large scale is purified by electrolysis, a process often called copper refining.
- Oxidation: The molten crude metal is exposed to hot air in a furnace. The impurities in the crude metal are oxidized with oxygen from the air. They escape as vapour or form a scum over the molten metal, which is then removed by skimming. However, this method is used only when the impurities have a greater affinity for oxygen than the metal. The method is applied in the manufacture of steel from pig iron and in the purification of tin and lead.
- Distillation:In distillation, the crude metal is heated in a furnace until the pure metal evaporates, leaving behind the impurities. The vapour is then collected and condensed in a separate chamber. This method forms an integral part in the extraction of zinc, cadmium and mercury. A further distillation, usually in vacuum, gives a very pure product.
- Formation of carbonyls: very pure nickel and iron are made by forming their volatile carbonyls, which are then decomposed by heating.
- Zone refining: This recently developed method is used to produce silicon and germanium of extreme purity. In this method, a small high-frequency induction furnace is placed round one end of a long rod of the metal and a thin cross-section of the metal is melted. The furnace is then moved slowly along the rod. Pure crystals of the metal separate from the melting metal but impurities remain in the liquid and are carried along to the other end.
The Extraction of Sudium from its Ore
Explain the extraction of sodium from its ore
Alkali metals are strong reducing agents and cannot be extracted by chemical reduction of their oxides or other compounds. The only possible method of their extraction is by electrolysis of their fused chlorides.Sodium is extracted industrially by electrolysis of either fused sodium hydroxide (Castner’s process) or fused sodium chloride (Down’s process), in which sodium chloride is electrolysed in the molten condition.
Electrolysis of sodium chloride by the down’s process
In this case, fused sodium chloride is used. And because the melting point of sodium chloride is high (about 800°C), calcium chloride is added to lower the melting point to about 600°C and thus economize on electrical power. The composition of the electrolyte is 40% sodium chloride and 60% calcium chloride.The Down’s cell (figure 8.1) used for the extraction of sodium consists of an iron box through the bottom of which rises a circular carbon anode. A ring-shaped iron cathode surrounds this carbon anode. The cathode is enclosed in iron gauze diaphragm, which also separates the two electrodes. At 600°C, the sodium and chlorine produced would react violently if allowed to come in contact. A diaphragm around the anode, which keeps the two products apart, prevents this.
During electrolysis, chlorine is librated at the anode and escapes via the hood. Sodium is liberated at the cathode, collects in the inverted trough placed over the cathode, rises up the pipe, and overflows into the storage tank, from which it is tapped off through the iron vessel.
The sodium metal is collected upwards in the Down’s cell because of its low density which makes it float over the mixture. The sodium metal from Down’s cell contains some calcium, which is also formed through electrolysis. The calcium crystallizes when the mixture cools and a relatively pure sodium metal is obtained.
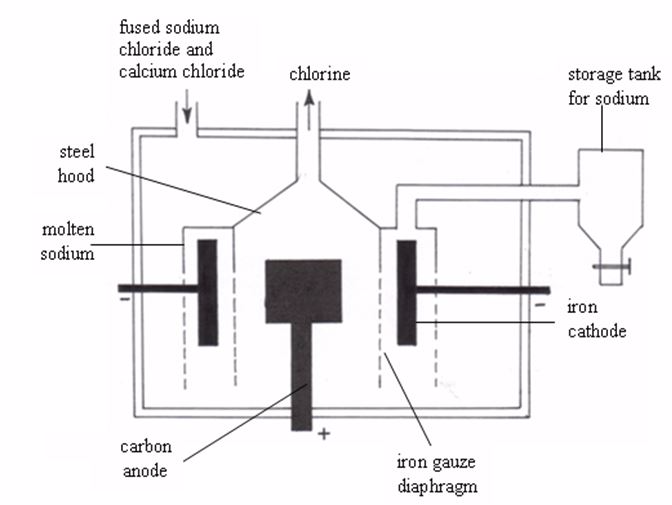
The Down’s cell
Fused sodium chloride produces Na+ and Cl- ions, where Na+ moves to the cathode and Cl-moves to the anode. The reactions taking place at the electrodes are as follows:

Chlorine gas is therefore formed at the anode while sodium metal is produced at the cathode.
2NaCl(l) →2Na(s) + Cl2(g)
Chlorine is a valuable by-product of the decomposition process.
Extraction of Metals by Chemical Reduction
The Extraction of Iron from its Ore
Describe the extraction of iron from its ore
Iron is only second to aluminium as the most abundant metal in the earth’s crust. Its chief ores are haematite, an impure iron (III) oxide, Fe2O3, which contains about 70% of iron; magnetite (or magnetic iron ore), triiron tetraoxide, Fe3O4, which contains 72.4% of iron; and spathic iron ore, iron (II) carbonate, FeCO3. It also occurs as limonite, Fe2O3.xH2O and as the sulphide in iron pyrites, FeS2. However, though abundant in the earth’s crust, iron pyrite is not used a source of iron. It is mainly used in the production of sulphuric acid.
To extract iron, three substances are needed:
- Iron ore: The chief ore is haematite. It is mainly iron (III) oxide, Fe2O3 mixed with sand.
- Limestone: This is mainly calcium carbonate, CaCO3.
- Coke: This is made from coal and is almost pure carbon.
The extraction of iron in a blast furnace
Before being introduced into the blast furnace, all forms of iron ore must be converted to the oxide, Fe2O3, by roasting in air.
4FeCO3(s) + O2(g) →2Fe2O3(s) + 4CO2(g)
4FeS2(s) +11O2(g) →2Fe2O3(s) + 8SO2(g)
Iron ore, coke and limestone are mixed together to give a mixture called charge. The charge is introduced into a tall tower called a blast furnace (figure 8.2). At the bottom of the furnace, hot air is blasted in through several pipes known as tuyeres. A well at the bottom of the furnace serves to hold the molten iron and slag until these can be run off. The charge is fed in continuously from the top.
Reactions that occur in the furnace
- At the bottom of the furnace where temperature is the highest, air attacks the coke to produce carbon dioxide.C(s) + O2(g)→ CO2(g)
- In the middle of the furnace, the rising up carbon dioxide gas is reduced by more coke, producing carbon monoxide.C(s) + CO2(g)→ 2CO(g)
- At the top of the furnace, carbon monoxide reduces iron (III) oxide to metal. Fe2O3(s) + 3CO(g)→2Fe(s) + 3CO2(g)
The molten iron trickles down the furnace and gathers at the bottom. Periodically, this molten iron is tapped off and run into moulds (or containers), where it is allowed to cool in long bars of about 1 metre long and 10 cm in diameter. At this stage, it is called ‘cast iron’ or ‘pig iron’.
The hot waste gases, mainly nitrogen and oxides of carbon, escape from the top of the furnace and are used to heat incoming air. This helps to reduce the energy costs of the process.
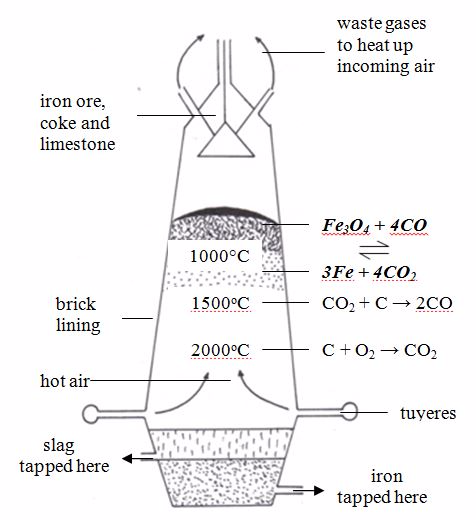
The Blast furnace
Action of limestone
The limestone, which is introduced together with the ore, is first decomposed at this high temperature to form calcium oxide.CaCO3(s)→ CaO(s) + CO2(g)
The main impurity in iron ore is sand, made of silicon dioxide (SiO2). This reacts with calcium oxide to form calcium silicate.CaO(s) + SiO2(s) →CaSiO3(l)
The calcium silicate, which is in liquid state, falls to the bottom of the furnace. This liquid, called slag (because it is less dense than the molten iron) is tapped off separately. Slag is a useful by-product. It is used for making roads, production of cement, and as a fertilizer.
Environmental Consideration
Environmental Destruction caused by Extraction of Metals
Identify environmental destruction caused by extraction of metals
Mining and mineral extraction is important for economic development and general human welfare. Without mining, we would have no cars, computers, handsets, washing machines or other equipment that we use to simplify our work and hence improve the quality of our lives. However, mining can cause many environment problems. The following are some of the environmental problems caused by mining:
- Land subsidence (sagging): Holes created due to underground mining cause land to sink (or subside). This is because the holes underneath the ground cause imbalance in weight of the soil above the ground. This may result to severe damage to buildings and other infrastructures such as roads, railway trucks and so forth.
- Poisonous substances: Poisonous compounds (for example of lead, cadmium and arsenic) are found in many ores. These may be washed into the soil and streams because of the mining process. If they happen to reach the water, they can kill fish and plant life, and can end up in your food as well. Gold extraction process makes use of mercury. If untreated effluent from the gold mine is directed to nearby rivers or streams, the metals may end up in fish, which might be someone’s food. Consumption of such fish can result to brain damage due to mercury contained in it.
- Large volume of waste: Large-scale mining operations inevitably produce a great deal of waste. This waste not only comprises of earth from the soil and gangue but also includes the toxic chemicals added to the ore to aid metal extraction. The waste material gets washed into streams and rivers. The sediment that builds up blocks rivers and alters their routes. This serves as a source of pollutants to natural water systems.
- Noise and dust: Mining activities produce a lot of noise and dust. Noise and dust can be caused by haulage trucks, rock blasting and crushing, drilling operations and heavy traffic. Everything for miles around the mine may get covered with dust.
- Big holes in the ground: Mineral extraction leads to boring of deep holes through the ground in the course of searching for rich ores. Huge amounts of rock are dug up to get a small amount of ore. For example, 1000 tonnes of rock may produce just 5 tonnes of copper. This leaves huge scars on the landscape (if it is opencast method) or huge holes underground (if it is underground mining).
- Great heaps of earth material: unwanted rock material, after the metal has been extracted from the ore, gets heaped up in tips. These are unsightly. They can be unstable and therefore dangerous. During heavy rains, a landslide is likely to occur, a catastrophe that often results to loss of life and destruction of property.
- Soil erosion: Before mining operation is carried out, the natural vegetation on or around the mining site is usually cleared up in order to give enough room to mining activities. The consequent removal of vegetation cover leaves the soil bare and, therefore, susceptible to erosion.
- Air pollution: Large-scale mineral extraction results to production of gases such as sulphur dioxide, carbon dioxide and other bad gases which are emitted to the atmosphere. These gases may bring about a green house effects and even cause acid rains.
Intervention Measures to Rectify Environmental Destruction
Suggest intervention measures to rectify environmental destruction
Different measures are taken to check the environmental degradation (problems) caused by mining activities. The following are some remedy measures taken to prevent such environmental destructions:
- Governments are getting ever tougher with mining companies about damage to the environment. Sadly, in developing countries like Tanzania where much mining takes place, laws may be less strict.
- Stern controls apply to the production of wastes that may be toxic or may cause environmental damage. Safety regulations and practices must be maintained to avoid the risk of accidental release of harmful materials.
- Mine reclamation activities are undertaken gradually with the levelling of the heaps of earth material, replacement of the top soil with a fertile one and planting of trees in the mined out areas. Care must be taken to relocate streams, wildlife and other valuable resources. Quarries and opencast workings can be reclaimed by the process of filling the holes with solid wastes. The eroded bare soil can be conserved by planting trees and grasses to serve as a soil cover, which would counteract the impacts of wind, running water, rain and animals to the soil.Reclaimed land can have many uses such as agriculture, forestry, wildlife, habitation and recreation.
- Dust levels can be controlled by spraying water on roads, stockpiles and conveyors. Other steps can also be taken including filling of drills with dust collection systems, and purchasing additional land surrounding the mine to act as a buffer zone. Trees planted in these buffer zones can also minimize the visual impact of dust, from the mining operations, to local communities.
- Noise can be controlled though careful selection of equipment and insulation, and enclosures around machinery.
- The poisonous and toxic substances used in metal extraction must be treated properly before being directed into rivers and streams. Alternatively, these materials may be drained into reservoirs where they can gradually percolate deep into the soil and evaporate into the air without causing much harm to the surrounding ecosystems. In some mines, absorbent carpets are spread on the surface of the ground to trap the toxic substances contained in liquid chemicals used for mining, hence preventing these chemicals from finding their way to water bodies.
EmoticonEmoticon